Generating high quality tools that are made to last
For over 30 years, Jackson has been consistently improving its LRTM moulding process, with massive advancements in recent years using its CaroC tooling product to take weeks out of the “Design to Production” turn-around. Combined with study and standardisation of tool features, in most cases the process is now complete inside of 1 week for the high-quality first article. This includes design, drawing, engineering.
The company’s clean, modern LRTM production line is set up primarily for internal mouldings, with the electrical side of the business being the main customer to both our moulding and tool making operations. Typical tool envelopes are 1-2m2 area, producing 4 to 5 parts per tool per day from “Low profile Tooling”.
To give an idea of longevity of production tooling, some of its legacy low profile tools have now produced in excess of 18,000 parts using this system. Contract moulding is also done in this facility, and is offered as a service in itself to clients.
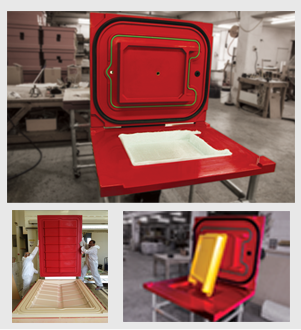